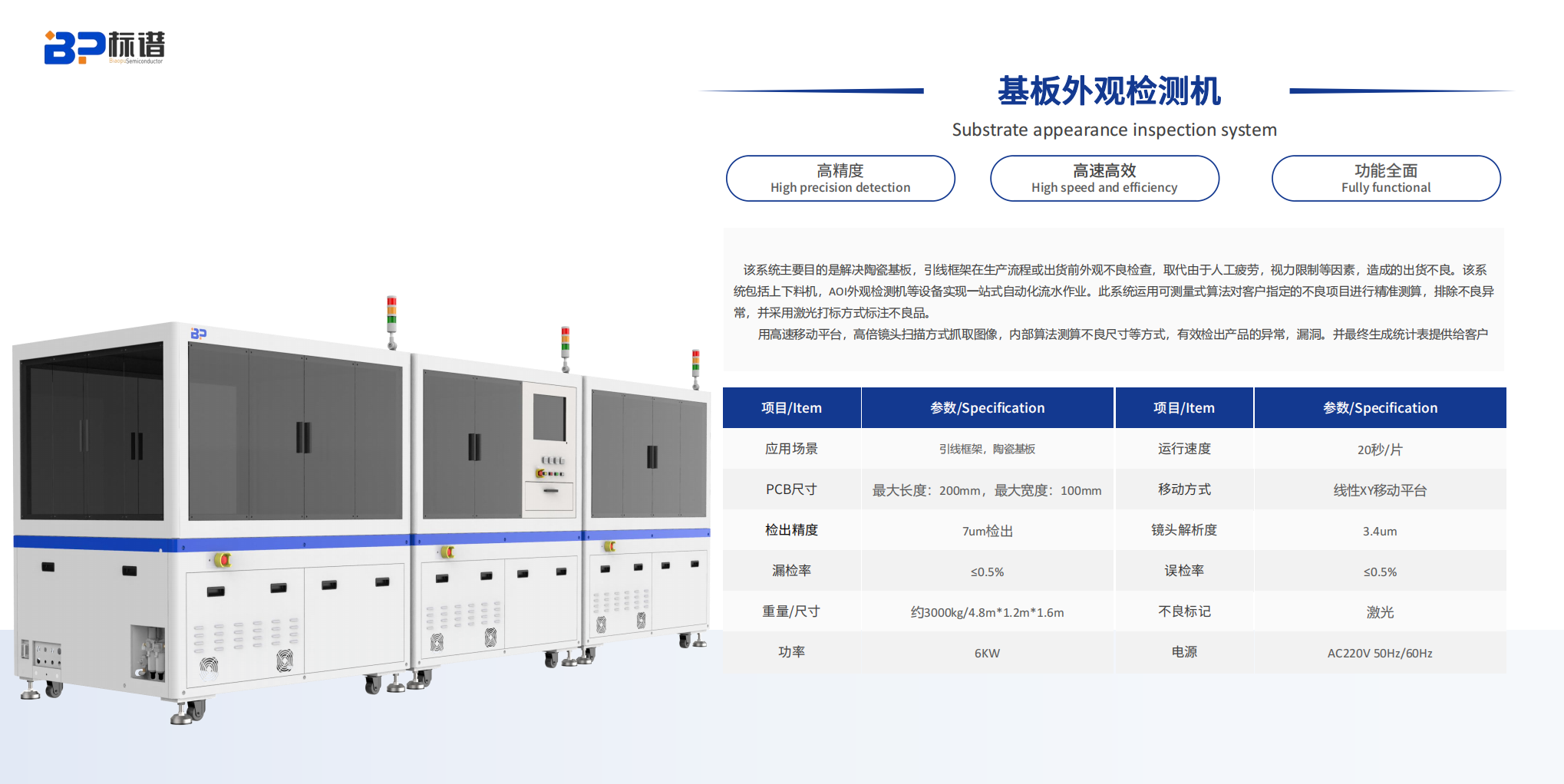
该自动化系统针对陶瓷基板与引线框架的生产质量管控,实现了从生产到出货前的全面外观不良检查,显著提升了检测效率与准确性,有效规避了因人工检查的主观性和疲劳导致的品质问题。以下是对该系统的详细解析:
系统概述
该系统集成了上下料机、自动光学检测(AOI)设备等多功能组件,构建了一站式自动化流水作业平台。其核心目标在于解决传统人工检查中存在的局限性,如视力疲劳、检查标准不一等问题,从而确保产品出货前达到高质量标准。
关键组件与功能
上下料机:实现自动化上下料,减少人工干预,提高生产效率。通过精准定位与抓取技术,确保每个待检产品都能准确无误地送入检测区域。
AOI外观检测机:作为系统的核心设备,采用高精度摄像头与图像处理技术,对产品表面进行全方位扫描。通过预设的算法模型,能够自动识别并区分各种不良项目,如划痕、污渍、缺损等。
可测量式算法:系统内置的可测量式算法,能够对客户指定的不良项目进行精准测算,包括不良的尺寸、位置等详细信息。这不仅有助于准确判断不良品的严重程度,还为后续的改进措施提供了数据支持。
激光打标:对于识别出的不良品,系统采用激光打标技术进行标记,以便后续分拣与处理。激光打标具有速度快、精度高、永久性等特点,确保了不良品的可追溯性。
高速移动平台与高倍镜头:为了捕捉更多细节,系统配备了高速移动平台与高倍镜头扫描方式。通过快速移动与高精度扫描,系统能够捕捉到产品表面的微小变化,从而更有效地检出潜在异常。
内部算法测算不良尺寸:除了直观的视觉检测外,系统还利用内部算法对不良尺寸进行精确测算。这有助于量化不良程度,为品质分析提供科学依据。
数据统计与反馈
系统最终会生成详细的统计表,包括不良品的数量、类型、分布等信息。这些数据不仅为客户提供了直观的品质报告,还为生产过程中的持续改进提供了重要依据。客户可以根据统计表中的数据,针对性地调整生产工艺或检查标准,从而进一步提升产品质量。
总结
该自动化检测系统通过集成先进的上下料机、AOI设备以及可测量式算法等技术手段,实现了陶瓷基板与引线框架生产流程中的高效、精准外观检查。它不仅提高了生产效率与产品质量,还为客户提供了全面的品质数据支持,有助于推动生产过程的持续改进与优化。